Category Archives: steel buildings
Pole Barn vs. Steel Buildings: 7 Reasons to Choose Steel Over Pole Barn Buildings
Traditional metal and/or wood pole barn buildings (those raised with no concrete foundation) are suitable for some people who want a quick and easy agricultural building, but many who choose them wind up playing the coulda-shoulda-woulda game when they realize what they could have gotten by choosing a Worldwide Steel Building instead.
If you’re weighing your options, think beyond the basic wood pole barn kits. Consider how much more you get — immediately and into the future — with a metal barn instead.
Check out these seven things you can get with a Worldwide Steel metal building that you can’t get with standard pole barn building construction:
1. Vertical Space (A.K.A. Clear Span)
Based on traditional pole barn construction, a pole barn can only rise so high for the sake of security in certain weather conditions. Even at limited height, it will tend to be more susceptible to the wear and tear of extreme weather.
With a steel building, the sky’s the limit for vertical space. The durability and strength of our steel trusses, girders, and framework offer incredible weather resistance. We like to say Worldwide Steel buildings can withstand anything Mother Nature has to offer.
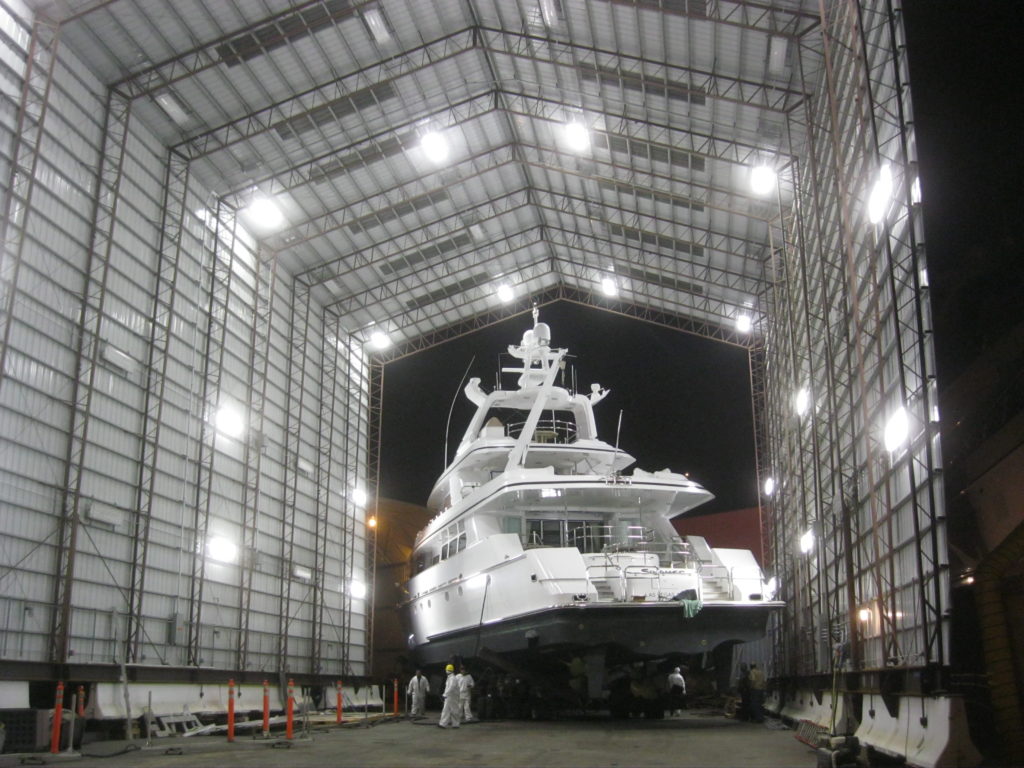
2. More Roofing Options
With a pole barn, roof options are limited to designs that coordinate with the layout of pole supports. In other words, things can get complicated and expensive if you want to get more creative than a typical pitched shed.
Choosing a steel building with a custom steel frame can give you the roof style you want whether it’s shed, hip, gable or gambrel. Want to throw in some skylights for natural lighting? A steel building can do that, too.
3. Open Floor Plan
The point of adding an auxiliary building is often to meet some sort of storage needs. If this is your main focus for your building, you’ll end up losing a lot of space with interior structural poles in the way. These also make it difficult to navigate large equipment. Prefab steel buildings help to get the most out of your potential storage space because they’re supported by trusses and framework that can create a completely open floor plan — no pesky steel columns impeding your open floor plan.
4. Mezzanine Ceilings
Because of the interference of support poles, it is practically impossible to integrate a mezzanine into a pole barn design.
If you need an elevated area in your structure to oversee work down below, or to create office or lounge space above, a steel building is your best option. Our prefab building kits can support lofted second stories for almost any purpose.
5. Customizable Extras & Add-Ons
Nearly endless extras and add-ons make steel buildings a more attractive option than standard pole barns. For instance, a steel building’s frame can handle the load for free-hanging eve extensions and multiple types of large mechanical garage doors, while a pole barn’s can’t.
These custom features can be used to increase the functionality of your building, while also giving you more options to personalize the overall style of your structure.
6. Longer Lifespan
Here’s where building material really comes into play: longevity. Why spend loads of money on a wooden pole barn building that will rot in the ground or be compromised by termites over the years? A dirt floor and wood post frames have nothing on the concrete floor and high-quality trusses and girts that make up a steel frame building. Choose the stronger option that’s built to last. Concrete piers and sound anchoring increase our steel building’s structural integrity, which means it’ll be stronger and last much longer than a pole barn … and with way lower maintenance costs.
7. Options For Growth
Think expansion may be necessary in the future? You’ll have to tear down that pole barn in order to expand. However, our steel buildings are easy to expand, thanks to the live trusses. This means that instead of starting from scratch in a few years, you can simply build upon what you already have!
So, what are you waiting for? The professionals at Worldwide Steel Buildings are waiting to answer your questions! Give us a call at (800) 825-0316 for more information on our industry-leading 50-year structural warranty and a free quote on your steel building price (here’s a hint — you might be pleasantly surprised by our metal pole barn prices).
Want to try it before you buy it? Take advantage of our FREE 3D Building Designer! Click here to get started.
How Much Would It Cost to Build a Mini Storage Building?
It’s a crazy world out there. The economy is uncertain, real estate costs and rent prices keep going up, and wages aren’t increasing at the same rate. These factors combined lead to a couple of different truths: First, many people are downsizing. They may realize they need a smaller square foot house than they’ve been living in. But then, what do they do with belongings they don’t want to part with? Second, a lot of other people are looking for ways to bring in more income and increase their cash flow. The more passive that income is, the better.
One idea? An independently owned self-storage business. Seems like a great idea, right? Fill a need for all the folks downsizing and start making money without many operating expenses beyond the development cost. Especially if you already own property (meaning you don’t have any additional up-front land costs to contend with), a collection of storage units, with various storage unit sizes to cater to different needs, sounds like a pretty great idea.
Still, no small business venture or construction project should kick off without thorough research. If you’re wondering about the average cost to build a mini storage building and turn your property into a mini self-storage facility, Worldwide Steel Buildings is here to get you started:
Assess the Situation
At first glance, the self-storage business may seem like a simple endeavor. After all, unlike most other businesses, there is no product ordering, no inventory tracking or storage, no spoilage or obsolescence issues, staffing and scheduling are minimal, and consumables and product liability are virtually nonexistent. But beware: silent waters often run very deep. Jumping head-first into the self-storage business because it looks easy may cause a bigger splash than you may be prepared to handle, especially considering the operating costs.
Make sure you’re educated on zoning restrictions for your property, prepared to handle climate control for your business’s buildings, and are thoroughly versed in occupancy regulations. Additionally, understanding the material costs involved in constructing your storage units is crucial (after all, desperate times call for desperate measures, and the cost of living continues to increase …).
Consider your Budget
Starting a self-storage building business as a startup can certainly be cost-effective up front and lucrative beyond that. Done correctly, it can also be pretty simple. We recommend starting modestly, with a limited, easy-to-handle number of single-story self-storage units in a couple of different unit sizes, considering both storage solutions and storage unit costs. When your business plan eventually calls for expansion, it will be easy to do so: especially if you choose a metal building kit for your self storage construction.
The building costs of a mini storage facility can vary greatly, but the total cost of building a mini storage facility does not need to break the bank. A prefab metal mini storage kit has proven to be among the most economical (not least because its DIY nature will require almost zero additional construction budget), and offers some of the most durable storage building systems around.
Then, once you’ve determined your initial investment (the building kit itself plus limited construction costs, including material costs), think about what you’ll need to set aside for maintenance and climate control. From there, you can begin to determine market rental rates and how many renters you’ll need to make your storage space business profitable.
Choose the Right Contractor
Worldwide Steel Buildings offers the highest quality storage unit kits at the lowest possible prices, optimizing storage solutions for every client. We offer a variety of shapes, sizes and finish options, designed specifically to maximize the use of your individual area.
Make your self-storage project your own by choosing your colors, door types, and roof pitches to suit the environment in your area and the storage needs of your potential customers.
Worldwide Steel Buildings works with customers in all fifty states, offering the best steel building solutions for every individual climate and elemental conditions, at the lowest possible mini storage building cost offered by anyone, anywhere! We can handle just about any storage need from private to commercial applications in the most economical fashion available, including open storage units for boat and recreational vehicle storage.
Plus, our metal building kits come with industry-leading, 50-year structural warranties, so you can feel confident your Worldwide Steel Building is a sound investment for today, tomorrow, and many years to come.
Ready to start your new business and get that increased cash flow rolling?
Contact Worldwide Steel Buildings today at (800) 825-0316 to find out more about Worldwide Steel Buildings mini storage packages and get a free quote on your new steel mini storage project.
Heavy Snow Loads and Steel Buildings
When it comes to constructing steel buildings, understanding and planning for heavy snow load is imperative, particularly in regions known for significant snowfall. The term “heavy snow load” refers to the weight of snow and its impact on buildings, which can vary depending on the type and amount of snow, as well as the structure’s design. Worldwide Steel Buildings recognizes the critical nature of this issue and prioritizes the design of metal buildings that can confidently withstand these challenging conditions. This blog delves into the importance of considering heavy snow load in the construction and maintenance of steel structures. We will explore the potential effects of snow accumulation on steel buildings, key design considerations to ensure structural integrity, best practices for maintenance, and the importance of adhering to building codes. Worldwide Steel Buildings is committed to delivering steel structures – from metal garages to large-scale storage buildings – that meet and exceed the demands of heavy snow load environments.
What Snow Means For Your Building Needs
Heavy snow loads can pose serious risks to steel structures. The weight of snow accumulation, especially during blizzards or heavy snowfall, can lead to potential structural damage. This includes stress on trusses, eaves, and the building roof. Safety concerns for occupants cannot be overstated, as the risk of collapse or damage increases under heavy snow load. Additionally, the economic impacts due to damage or downtime can be significant, especially in commercial storage buildings or steel garages.
The good news is that steel and metal buildings from Worldwide Steel are built with what it takes to handle the heavy and harsh snow pile-ups required in each area of the country. In fact, it is found that metal and steel buildings may actually be better suited to handling higher snow loads than traditionally framed homes.
Key Considerations for Designing Steel Buildings in Heavy Snow Load Areas
In designing buildings for areas prone to heavy snowfall, Worldwide Steel Buildings considers several key factors. Structural reinforcement is a crucial aspect, including the use of sturdy trusses and robust building kits. Roof design, particularly the pitch, plays a significant role; a steeper roof pitch can help reduce snow buildup, enhancing the building’s ability to shed snow. Professional engineering evaluations are essential to ensure compliance with building codes, considering factors like ground snow load, wind load, and roof snow load.
Best Practices for Maintaining Steel Buildings in Heavy Snow Load Areas
Proper maintenance is essential for steel buildings in heavy snow load areas. Effective snow removal strategies and the use of specialized equipment can prevent issues like ice dams and excessive snow accumulation. Regular inspections are important for identifying and addressing damage or wear, especially after the winter season. Proactive maintenance, backed by the comprehensive warranty offered by Worldwide Steel Buildings, is vital for ensuring the longevity and safety of metal structures, including garages, carports, and larger buildings.
Conclusion
Snow is the heaviest and most dangerous when it is compacted. If you live in a climate where compacted snow could develop, then it is important to take weather precautions under consideration when building your structure. Compacted snow is heavy due to the layers of ice that form in between the layers of snow. Be educated about the weather risks in your area and know what you need your building to stand up against when making your choice of materials. Steel and metal buildings can be used for garages, workshops, and residential and commercial needs, and are easily insulated to make the inside just as comfortable as the outside is sturdy.
Recognizing the importance of heavy snow load considerations in the design and maintenance of steel buildings is crucial. Worldwide Steel Buildings is dedicated to providing structures that are not only capable of withstanding the challenges of heavy snowfall but are also designed with safety, longevity, and efficiency in mind. We invite potential clients to consult with our team of building specialists and experts to benefit from our extensive experience in creating durable, reliable steel buildings for various needs and environments.
Are you planning a new building project in an area with heavy snowfall? Don’t let the winter weather catch you off guard. Contact Worldwide Steel Buildings now to discuss your project needs. Our team of building experts and specialists are ready to guide you through every step of the process, ensuring your structure is perfectly suited to withstand heavy snow loads. When the snow does fall, you want to rest assured that you have the strongest building design in the business. From small garages to massive work equipment sheds, you can get the confidence you need that you have a solid building that will stand up no matter the weather.
Steel Building Prices
At Worldwide Steel, we’ve noticed something interesting. Often, when potential customers are researching their new building project, they’re drawn to a metal building (and for good reason — there are so many benefits to a steel structure). But they’re immediately wary of metal building prices. For some reason, the price of steel has gotten a reputation for being more volatile than the price of other building materials. And yes, the price of steel does fluctuate along with the economy. But so does the price of every other material. Look at what happens to the price of wood, tile and brick as the economy fluctuates!
So rather than looking at just the cost of building materials, it makes sense to consider the cost of metal building kits against traditional construction from start to finish. And when you do that, you’ll see steel building cost benefits begin with construction and last a lifetime.
Affordability is Key
Steel and metal buildings are cost-effective from the very beginning. Because they are so customizable, you’re largely in control of the final price tag. With Worldwide Steel, you can design something well within your price range. Of course, larger buildings with more add-ons will come at an additional cost, but your design will be very affordable per square foot regardless of building size.
From there, it is up to you what materials you use to finish the building, which means that you have even further control over the total cost. Exterior finishes are available in sheet metal, vinyl, stucco, wood or brick, and while all offer enhanced durability and strength, each can provide your building with a unique finishing touch.
You’ll also see metal building cost savings beginning with construction costs. Because your metal building is so simple to erect, it will go up quickly with minimal construction needed. That means a smaller crew, fewer days dedicated to building, and less need to rent equipment, all of which ultimately add up to a more affordable construction process.
Another factor that makes the steel building construction process so affordable is how comprehensive Worldwide Steel building kits are. Our steel building kits include everything necessary for your metal building, from the trusses to the last fastener. That means:
- Buildings are able to be erected in minimal time, oftentimes within just a matter of days
- Steel buildings can be constructed with unskilled labor, thanks to comprehensive building kits and an easy-to-follow manual. When putting together a building is truly a simple, DIY task, you’ll save big on labor costs.
- No heavy equipment is necessary for construction, which further reduces labor and rental
- Steel kits are lightweight, which makes for an easier construction process
While it can be tough to think past the initial costs when you’re about to make a big financial investment, it’s crucial — especially when it comes to a new building. When you’re investing in something you’ll own and maintain for years to come, the cost of that maintenance is a major factor in the cost of the building over its lifetime.
Steel frame buildings are extremely low-maintenance, durable and energy-efficient, all of which means they’re cheaper to own over the decades as well as upfront. Because our steel frames are designed to stand up to harsh winds, heavy snow loads and other environmental concerns, they’re less likely to fail under normal circumstances. They’re also less susceptible to common annoying building issues, like rot and insect infestation.
We’re so confident in our building systems that each one is backed by an industry-leading 50-year structural warranty.
Affordable Steel Buildings From Worldwide Steel
Ready to see exactly how much your prefab metal building will cost? Worldwide Steel Buildings offers top-of-the-line steel building kits at affordable prices. Call us at (800) 825-0316 for a free building quote, or request a quote online.
A Worldwide Steel Buildings expert can help you determine what size and material types are best for your project (for example, a metal barn used to house animals may have different requirements than a metal garage built to store heavy machinery). That means you won’t have to waste precious funds on unnecessary building materials or put money into a project that doesn’t meet your needs.
Contact us for more information about steel building prices! Financing options are available to make the construction process even more affordable.
Steel Workshops for Sale
Worldwide Steel Buildings offers the best deals on steel buildings, including steel garages, sheds and workshops, making it an easy choice when it comes to finding the best building options and materials for your workshop needs.
There are a few things that you want to look for when choosing the right material for your workshop. These include:
- Durability
- Stability
- Reliability
Steel buildings offers all three of these fundamental needs, putting other options like wood to rest.
Steel: The Best Choice for Workshops
Workshops are an extension of your home and workplace. They are an environment dedicated wholly to the hobbies, hand crafts and projects that you put your time and energy into working on. Whether your workshop is for personal projects or is necessary out of industrial concerns, you want to make sure that you find a workshop that will stand up to the elements and keep your materials safe and secure. Steel workshops are not susceptible to termites and other insects, the walls don’t break down and crack after time and exposure to moisture, and they are easily reinforced to make theft incredibly difficult.
Of course, there are other reasons why steel is the ideal building material, well beyond the security of what goes inside the building. Steel is a flexible building material that can be manipulated under certain forms of pressure to fit the design that you need. Once in place, the steel is not going to budge. However, as you are designing your steel workshop you can take into account certain needs, such as higher ceilings or smaller alcoves.
Steel workshops are also one of the most affordable options on the market when it comes to the development of smaller buildings. There is a wide selection of carports and steel reinforced walls that makes purchasing a steel workshop simple. What is more, the construction is also affordable, simple and quick, which means that you can get to work in your workshop faster than you would be able to with a traditional building model.
Steel buildings can be upgraded, updated and remodeled as needed to accommodate future needs. The nature of steel buildings makes it easy to adjust the building size to the needs of the property, and as the property availability changes, so can the size of the steel building.
If you are looking for a new workshop, steel building construction is the way to go. Contact us for more information.
Common Complaints that Worldwide Steel Buildings Never Hear
After 30 years in the business of selling and manufacturing steel buildings, we’ve talked to a lot of people who were unhappy with products they bought from other dealers. There may be a lot of vendors out there, but you need to pick a steel building company who has the experience and professionalism to deliver a high-quality and affordable product. Otherwise, you may find yourself in the same position as the people who come to Worldwide Steel Buildings with complaints about the other guy. So you know what we mean, here are four of the most common complaints of steel building owners and how buying from Worldwide Steel Buildings steers you clear of those pitfalls.
Structures That Are Not Built to Last
At Worldwide Steel Buildings, the most common complaint we hear is that other dealers aren’t selling structures that are built to last. We take quality very seriously at Worldwide Steel Buildings and enshrine high-quality standards into each step of the process. Worldwide uses only American recycled steel and trusses are built on jig tables to maintain the same quality on every truss. Each truss is then inspected prior to being dipped in our rust inhibitor / primer tank.
We stand by the quality of our work vigorously. Worldwide Steel Buildings offers a 50-year structural warranty, far longer than the standard 1-2 year warranties offered by other steel building companies. Additionally, the premium sheet metal we use also offers a 40-year warranty, giving consumers a maintenance-free building with the durability to last a life time.
Paying Too Much
Another complaint we hear far too often is that other dealers overcharge customers for the quality of product they produce. At Worldwide Steel Buildings, we pride ourselves on being both high-quality and affordable. Because of our 30 years of experience and team of experts, Worldwide Steel Buildings is uniquely able to deliver long-lasting building packages at a truly affordable price. Our consultants work with our architects and engineers to put together the highest performance building package at the lowest cost; making our buildings the best value available. And we mean affordable to everyday consumers as well as businesses. Over the years, Worldwide Steel Buildings has provided economical solutions to hundreds of commercial, residential, agricultural and industrial applications.
Structures That Don’t Meet Local Requirements
When designing structures that must withstand the elements, cookie cutter solutions just won’t do. A building that would be structurally sound in one part of the country may not be in another. A structure built to withstand hurricane winds may not be built to withstand heavy loads of snows. It may even be a legal matter, so it’s important to find a manufacturer that’s experienced at navigating the various rules of each state and jurisdiction. All of the steel buildings Worldwide manufactures are designed to the required loads and codes for the location they are erected. We have buildings in all 50 states that have been designed for high winds or heavy snows. In nearly 30 years, we have never had a building fail do to structural design.
Structures that Don’t Meet Needs of Clients
A common complaint we hear from customers who first bought from other dealers is that the structure doesn’t fit their needs. This could be because the design had less usable space than they originally thought, there wasn’t a plan that suited their needs, or because their needs changed over time. These aren’t reasons for complaints when a customer buys a structure from Worldwide Steel Buildings. Every Worldwide building has 100 percent usable space clear to the peak. There are also many different modification options so the structures can be designed for any type of application. A second floor or loft storage can be added with a Worldwide-exclusive bar joist system. There’s a 14’ self-supporting overhang for additional roofed storage outside the building. And the building can grow with the needs of the user. All Worldwide Steel buildings offer an expandable end wall for future expansion.
When you buy from a qualified steel buildings company like Worldwide Steel Buildings, there’s no reason for complaints. From start to finish, we strive for high-quality, affordability, and accountability. To learn more about our products, warranties, or to get started, visit our contact page.